When I started out in business analysis (more than 20 years ago!), my role was all about “process improvement”. Essentially, I was tasked with finding ways to slash operating costs through headcount reductions. While it wasn’t generally stated in such bald terms, the clues – having to state the likely FTE saving of each proposed idea – were there.
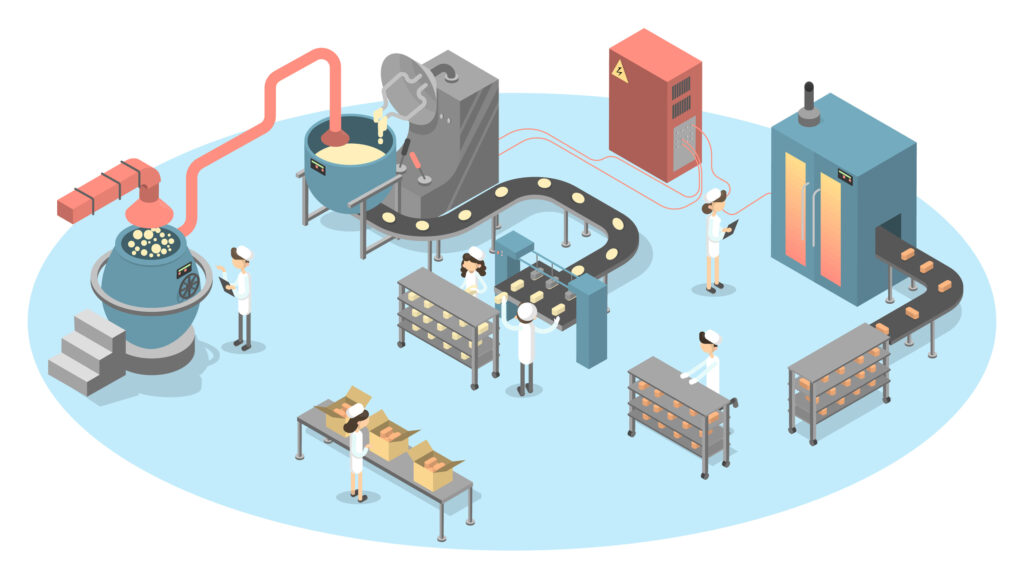
These days, organisations are still looking for ways to improve how they do things. Some have teams tasked with “continuous improvement”. Others will bring in clever consultants to seek out “efficiencies” (another slippery term). The business cases for projects and products will invariably claim that things will be better. “Digital transformation” is another catch-all term that let’s people assign their own meaning.
Identifying “process improvement” opportunities
I’m one of those people that constantly angsts about finding using selecting the best word to convey what I mean. Using the phrase “process improvement” can be far too general and risks talking at cross-purposes. There are many ways a process can be “improved”, and it’s important to be specific and to ensure we’re not limiting the range of opportunities we might find.
In discovery workshops, I often use a rough-and-ready scoring exercise with stakeholders to explore how a process is performing from several different angles:
Effectiveness
Processes can be improved by making them deliver better quality (or more valuable) outputs, producing the right outputs and the right time, or by producing more outputs for the same inputs.
Customer experience
Are there lots of complaints? Is feedback often negative? Do you customers often experience delays or find it difficult to get what they need?
Making it easier, quicker, or less painful for customers to use the process will always be welcomed, and can bring repeat custom, increased spend, and word-of-mouth recommendations.
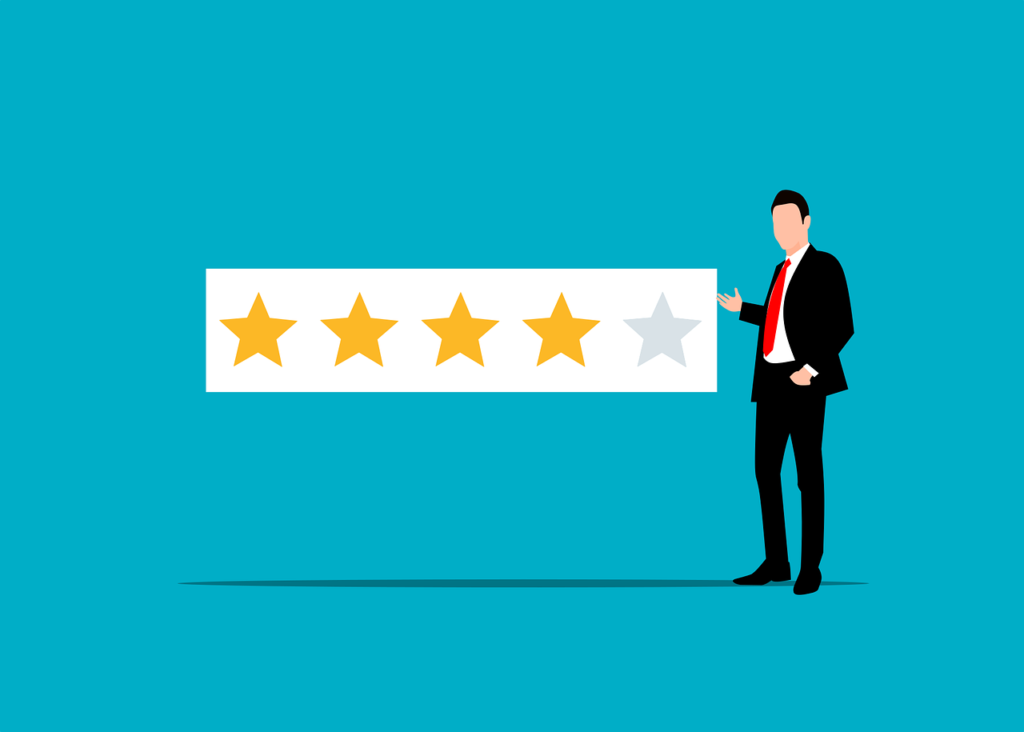
Staff experience
Do your people hate performing this process? Is it creating friction between teams? Is it overly complex or challenging? Do people have the right tools and information at their disposal?
Talk to those that actually do the work, and you’ll quickly find a host a ideas for making tasks less onerous, frustrating, or stressful. This aspect is rarely given the attention and support it deserves!
Time, effort, and materials
This is what people often mean when they use the word “efficiency” – they want to cut costs. That’s fine and healthy, but let’s be specific and honest!
Reducing the work required or the materials used up makes the process cheaper to perform, and this can have a direct impact on an organisation’s bottom-line.
The LEAN categories of waste provide a great lens for identifying opportunities to make savings.
Roles + resourcing
Do we have the right people doing the right tasks, and are we providing the right level of resources for the task at hand?
Stability + standardisation
Is the process clearly defined? Are standards and expectations clear? Do the same inputs always produce the same outputs?
Making a process more predictable and reliable can be a great way of reducing failure demand.
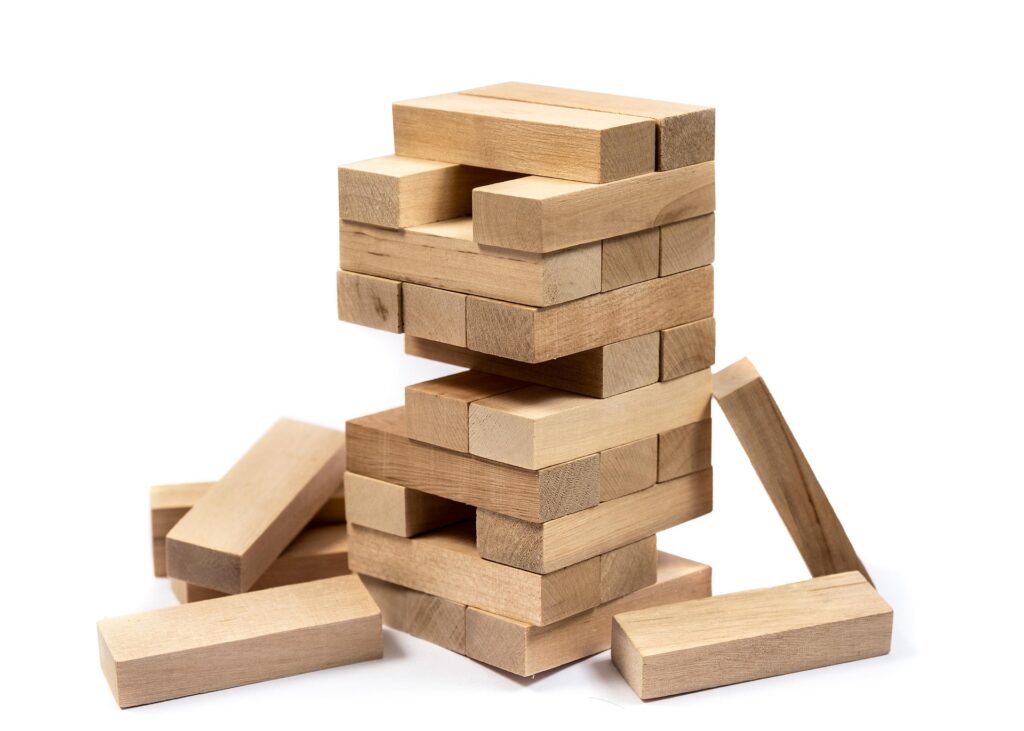
Monitoring + oversight
If nobody is monitoring and directing performance, how will we ensure we’re achieving the best results? Find out whether the right data is available, and whether anyone is actually looking at how things are working!
Reporting is one of my personal bugbears – organisations frequently adopt inappropriate reporting methods. Lists, totals, trends, and projections should be chosen with care. Weekly/monthly reports, dashboards, and alerts/notifications all serve different purposes. It’s crucial that those in charge get the right information at the right time.
Risk + controls
Business processes can present all kinds of risk – financial loss, reputational damage, physical injury, or data breaches, to name but a few.
Look at the different types of risk in the process, and evaluate whether controls are appropriate to likelihood and impact (and whether they’re actually working!). Do we have the right detective and preventative controls?
Managing risks more effectively can be a great way to unlock other categories of process improvement – less time fighting fires means more time for making things better!
Future viability
Things might be ok today, but can we carry on like this? What trajectories can we see in the data? What external factors will influence what’s needed in the future (hint, PESTLE is a great workshop tool here!).
Process improvement can mean finding ways to “future-proof”, such as adopting newer technology or building-in resilience.
Choosing what to improve
Stakeholder groups will often provide differing insights into where a process might require improvement. Process owners will typically have a different perspective from teams that actually do the work. Customers, suppliers, partners, and senior leaders will all have their own ideas about what’s working and what needs to be better. Look upstream and downstream too!
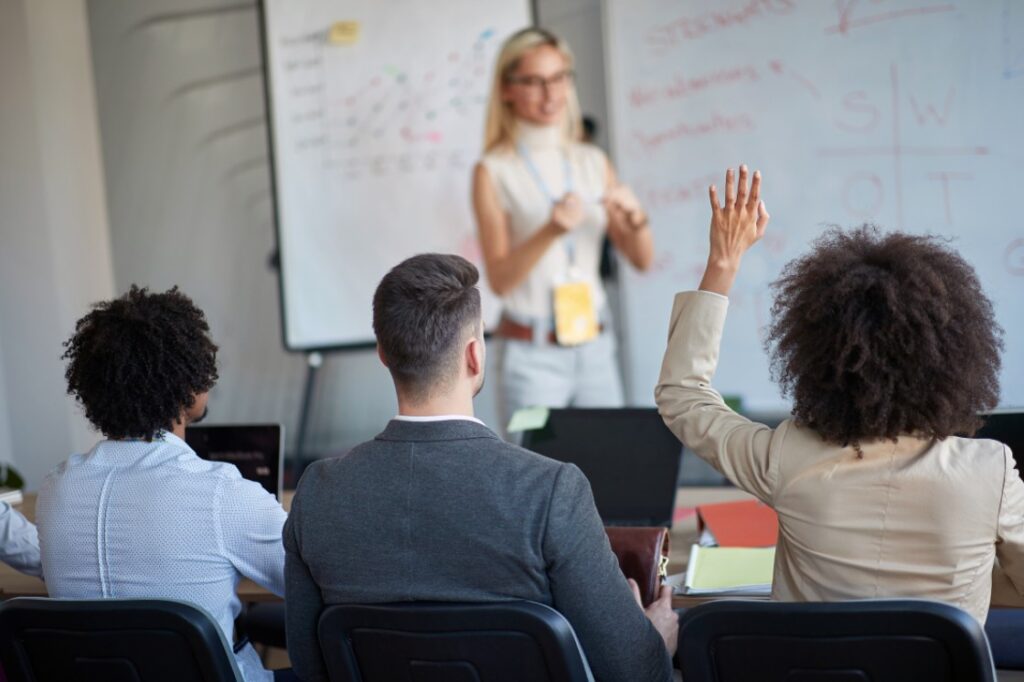
Seek out evidence to validate problems and gaps, and establish what KPIs or other measures will be used to establish the current position and track improvements.
There’s rarely enough time or money to address everything! Evaluate ideas against the organisation’s strategic goals to prioritise where process improvement efforts should be spent. If the wider strategy is all about delighting customers or attracting talent, bearing-down on costs may not be a winning approach – conversely, chasing quality-of-life improvements may get short shrift if belt-tightening is high on the agenda. Often, any given change can unlock several kinds of benefit, so it’s always useful to have explored a range of angles.
Being specific about the kinds of improvements being pursued, and aligning these to the organisation’s strategy, is key to getting consensus on the way forward and ensuring everyone is pulling in the same direction.
Of course, identifying the potential for process improvement is really just the first step. Once you know what needs to be better, you can start exploring the levers-to-pull and buttons-to-press: changes to process steps, roles and responsibilities, resourcing, technology and tools, business rules, process controls, information, supply of materials, and physical location – to name just a few!